A Place For Everything, and Everything in its Place
How a Simple Phrase Revolutionized My Approach to Inventory Control
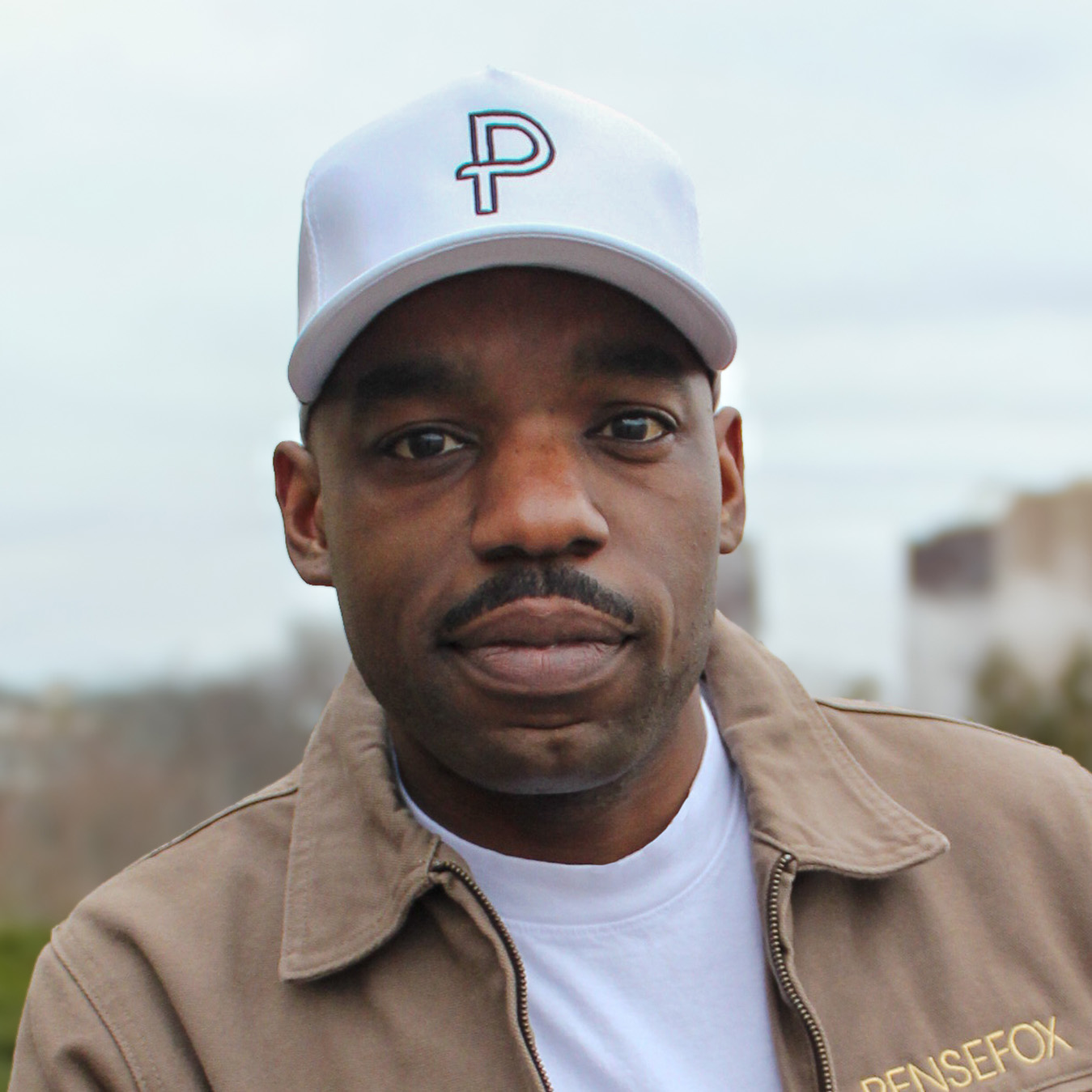
.png)
During my time at Liberty Safe, the Division President, my boss turned mentor, had this saying he’d repeat almost daily: “A place for everything, and everything in its place.” At first, I couldn’t stand hearing it. It was one of those phrases that lingered in the air long after the conversation ended, taunting you as you went about your day.
But like most great lessons, it wasn’t until later that the true meaning sank in. Let me back up a bit to explain how I ended up there and why those words have stuck with me to this day.
The journey to Liberty Safe wasn’t something I had mapped out. After my freshman year of college, I moved in with a couple of friends and picked up a string of odd jobs to make ends meet. I was also taking online classes to keep my mom happy. One day, my roommate suggested I apply at his job, a warehouse that needed extra hands. With nothing to lose, I went for it.
On my roommate’s word alone, I was hired, but that’s where the easy part ended. My first day was a humbling experience. I didn’t know the difference between a pallet and a pallet jack, and my hours reflected my steep learning curve, but I stuck with it. Over time, the company grew, and so did I.
I eventually left school to work full-time and committed to climbing the ladder. Starting as a Warehouse Associate, I worked my way up to an unofficial Production Supervisor role. At just 21, following Liberty Safe’s acquisition of my mentor's company, I earned another promotion and became the first employee in Liberty’s history to have their undergraduate degree funded by the company.
Looking back, I realize what a leap of faith that was for my boss. He saw something in me worth investing in, and I’ve always been grateful for his belief in my potential.
My mentor didn’t just teach me about operations; he modeled what it meant to be a leader. He never raised his voice, led by example, and treated everyone with respect, regardless of their title. His meetings were meticulously planned, and his commitment to excellence was unmatched.
If my work ethic comes from my mom, then my leadership style is a reflection of him. He taught me that the best managers inspire their teams through action, not fear.
When he felt I was ready to “run the show,” he started coaching me on thinking in more efficient, strategic ways. That’s when the phrase “A place for everything, and everything in its place” became his mantra.
At first, it annoyed me. Every time he said it, I rolled my eyes internally. Finally, I asked him outright, “What does that even mean?”
His response was simple: “It’s exactly what it sounds like, David: a place for everything, and everything in its place.”
I thought about it on my drive home, and then it hit me—he was talking about inventory.
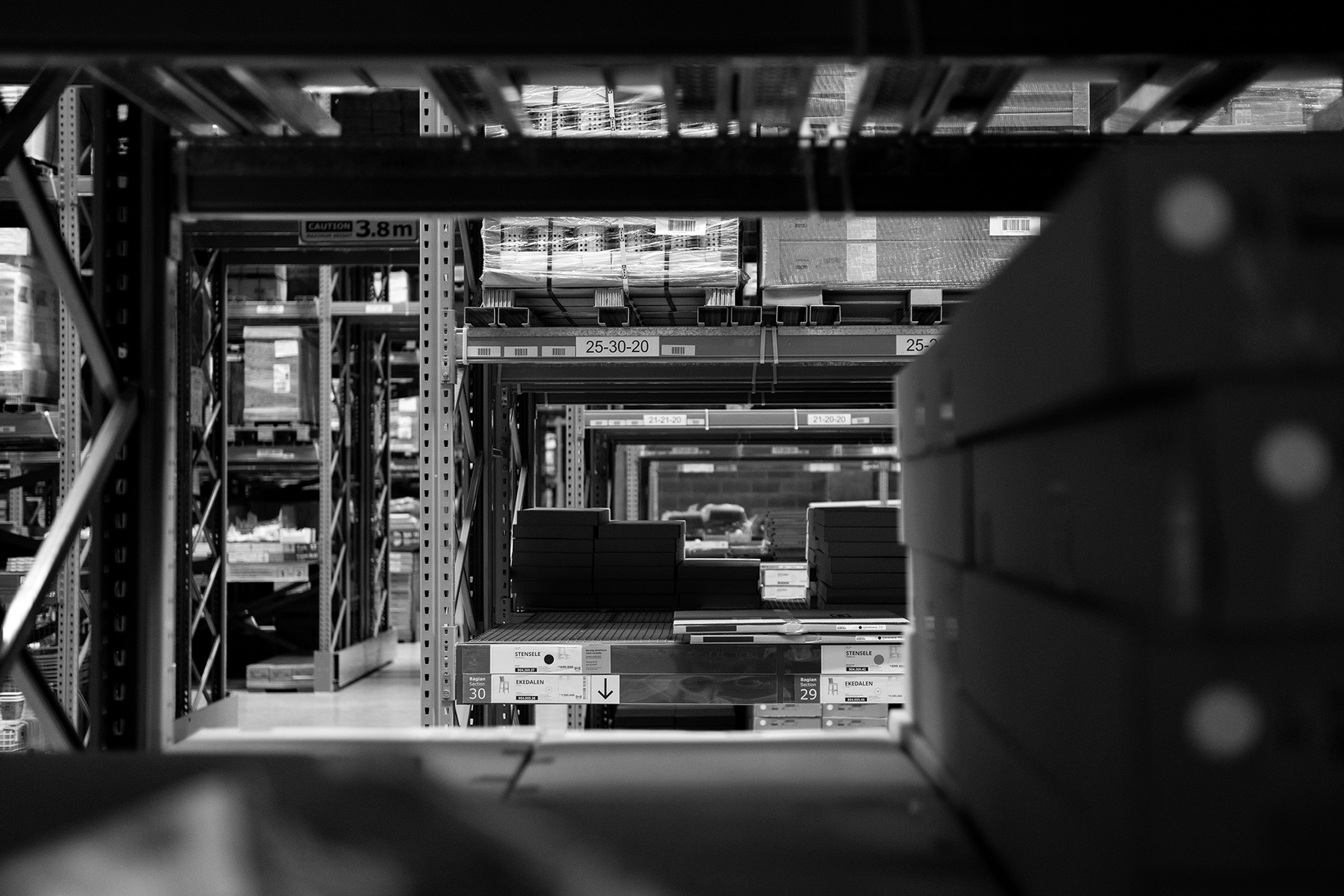
In manufacturing, inventory is the heartbeat of the operation. Without effective inventory management, everything falls apart. It’s like trying to cook dinner without checking what’s in the fridge. You’ll either have to scramble for substitutes, run to the store, or scrap the meal entirely.
When we moved into a new facility, the importance of “a place for everything” became crystal clear. Our team completely overhauled inventory management. Raw materials were grouped and stored on one side of the warehouse; finished goods were on the other. Every sub-assembly area had dedicated raw and finished storage to keep production lines running smoothly.
We took it further:
- At the end of each shift, associates reset and restocked workstations, ensuring the next shift started fresh.
- Daily cycle counts resolved variances immediately, ensuring our records were almost always accurate.
The results were staggering. When I started, our team was producing 20–25 units daily. By the time I left, we had scaled to 350–375 units per day.
Of course, other key factors such as genius-level engineers and loyal, dedicated employees contributed to that growth. But our success was dependent on effective inventory management. Without it, production stalls, costs skyrocket, and lead times become a guessing game. With it, operations gain stability, insight, and the ability to plan for success.
What started as an annoying phrase turned into one of the most important lessons of my career. Today, as I work with organizations, I carry that mindset with me. Whether it’s optimizing workflows, organizing warehouses, or building stronger teams, the principle remains the same: “A place for everything, and everything in its place.”
It’s more than a phrase; it’s a philosophy. It’s about creating systems that empower people to succeed, and it’s proof that the best lessons don’t just stick—they transform how you approach everything.
Here’s to the mentors who push us, the lessons that linger, and the transformations that follow.